Understanding Desifake: The Rise Of Digital Fabrication In Modern Industries
Mar 20 2025
Digital fabrication has revolutionized the way industries approach manufacturing and production processes. From 3D printing to advanced CNC machining, this transformative technology is reshaping the landscape of modern industries. Known as "Desifake" in certain circles, this concept highlights the increasing reliance on digital tools and software to create intricate designs and prototypes, driving innovation across sectors.
As we delve deeper into the era of Industry 4.0, the significance of digital fabrication cannot be overstated. It enables businesses to streamline operations, reduce costs, and enhance product quality. This article explores the rise of digital fabrication, its impact on various industries, and its potential to shape the future of manufacturing.
Through this comprehensive guide, we aim to provide valuable insights into the world of Desifake and digital fabrication. By understanding the principles, applications, and benefits of this technology, readers can harness its power to drive growth and innovation in their respective fields.
Read also:Does Mark Harmon Have Cancer Unveiling The Facts And Clearing The Rumors
Table of Contents
- What is Desifake?
- History of Digital Fabrication
- Key Technologies in Digital Fabrication
- Applications in Various Industries
- Benefits of Digital Fabrication
- Challenges and Limitations
- Future of Digital Fabrication
- Case Studies: Success Stories in Desifake
- Ethical Considerations in Digital Fabrication
- Conclusion
What is Desifake?
The term "Desifake" refers to the integration of design and fabrication processes through digital tools and technologies. At its core, digital fabrication involves the use of computer-aided design (CAD) software and advanced machinery to create physical objects from digital models. This approach allows for greater precision, flexibility, and customization in manufacturing.
Defining Digital Fabrication
Digital fabrication encompasses a range of technologies, including 3D printing, CNC machining, laser cutting, and robotics. These tools enable manufacturers to produce complex designs with minimal waste and maximum efficiency. As industries continue to embrace digital fabrication, the boundaries of what can be achieved in manufacturing are constantly being pushed.
History of Digital Fabrication
The origins of digital fabrication can be traced back to the mid-20th century, with the development of numerical control (NC) machines. Over the decades, advancements in technology have transformed this field, leading to the sophisticated systems we see today.
Key Milestones in the Evolution of Digital Fabrication
- 1950s: Introduction of NC machines
- 1980s: Emergence of CAD software
- 1990s: Development of rapid prototyping techniques
- 2000s: Rise of 3D printing and additive manufacturing
Key Technologies in Digital Fabrication
Several technologies underpin the success of digital fabrication. Each plays a critical role in enhancing the capabilities of modern manufacturing processes.
3D Printing
3D printing, also known as additive manufacturing, involves building objects layer by layer from digital models. This technology is widely used in industries such as aerospace, automotive, and healthcare.
CNC Machining
Computer numerical control (CNC) machining uses automated tools to cut and shape materials with high precision. It is commonly employed in the production of metal components and complex parts.
Read also:Matts Offroad Recovery Family A Comprehensive Guide To Their Adventure And Legacy
Laser Cutting
Laser cutting technology uses high-powered lasers to cut through materials like metal, wood, and plastic. Its accuracy and speed make it an ideal choice for various applications.
Applications in Various Industries
Digital fabrication has found applications across a wide range of industries, each leveraging its unique advantages to drive innovation.
Automotive Industry
In the automotive sector, digital fabrication is used to create prototypes, custom parts, and tooling. This reduces development time and costs while improving product quality.
Aerospace Industry
The aerospace industry benefits from digital fabrication through the production of lightweight components and complex structures. This technology enables manufacturers to meet stringent performance and safety requirements.
Healthcare Industry
Within healthcare, digital fabrication is revolutionizing the creation of medical devices, prosthetics, and implants. Personalized solutions can now be developed with unprecedented accuracy and efficiency.
Benefits of Digital Fabrication
The adoption of digital fabrication offers numerous advantages for businesses and consumers alike. These benefits include:
- Increased efficiency and productivity
- Reduced material waste and environmental impact
- Enhanced customization and personalization options
- Improved product quality and consistency
- Lower production costs and faster time-to-market
Challenges and Limitations
Despite its many advantages, digital fabrication is not without its challenges. Some of the key obstacles include:
High Initial Costs
Investing in digital fabrication technologies can be expensive, particularly for small and medium-sized enterprises (SMEs). However, the long-term benefits often outweigh these initial costs.
Skills Gap
There is a growing need for skilled professionals who can operate and maintain digital fabrication equipment. Training programs and educational initiatives are essential to address this skills gap.
Future of Digital Fabrication
The future of digital fabrication looks promising, with ongoing advancements in technology and increasing adoption across industries. Emerging trends such as artificial intelligence (AI), robotics, and the Internet of Things (IoT) are set to further enhance the capabilities of digital fabrication systems.
Predictions for the Next Decade
- Greater integration of AI-driven automation in manufacturing processes
- Development of new materials and composites for digital fabrication
- Expansion of digital fabrication into emerging markets
Case Studies: Success Stories in Desifake
Several companies have successfully implemented digital fabrication technologies, achieving remarkable results. These case studies highlight the transformative power of Desifake in modern industries.
Case Study 1: GE Aviation
GE Aviation has leveraged 3D printing to produce fuel nozzles for jet engines, reducing weight and improving fuel efficiency. This innovation has led to significant cost savings and environmental benefits.
Case Study 2: Ford Motor Company
Ford has embraced digital fabrication to accelerate its product development cycle. By using 3D printing for prototyping, the company can bring new models to market faster and more efficiently.
Ethical Considerations in Digital Fabrication
As digital fabrication continues to evolve, it raises important ethical questions that must be addressed. These include issues related to intellectual property, environmental impact, and workforce displacement.
Intellectual Property Concerns
The ease of replicating digital designs raises concerns about intellectual property theft. Manufacturers must implement robust safeguards to protect their proprietary designs and innovations.
Conclusion
In conclusion, understanding Desifake and the rise of digital fabrication is crucial for businesses seeking to thrive in the modern industrial landscape. By embracing this transformative technology, companies can unlock new opportunities for growth and innovation.
We encourage readers to explore the possibilities of digital fabrication further and consider how it can benefit their own operations. Feel free to leave a comment or share this article with others who may find it valuable. For more insights into cutting-edge technologies, be sure to check out our other articles on the latest trends in manufacturing and beyond.
Data Source: Statista, McKinsey & Company, GE Aviation.
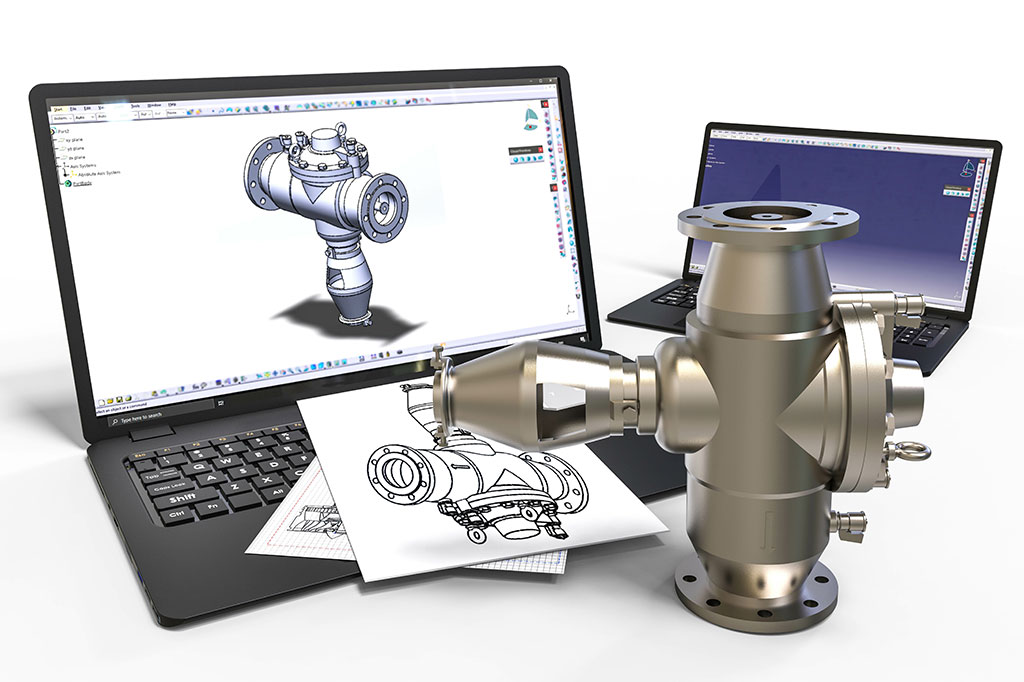
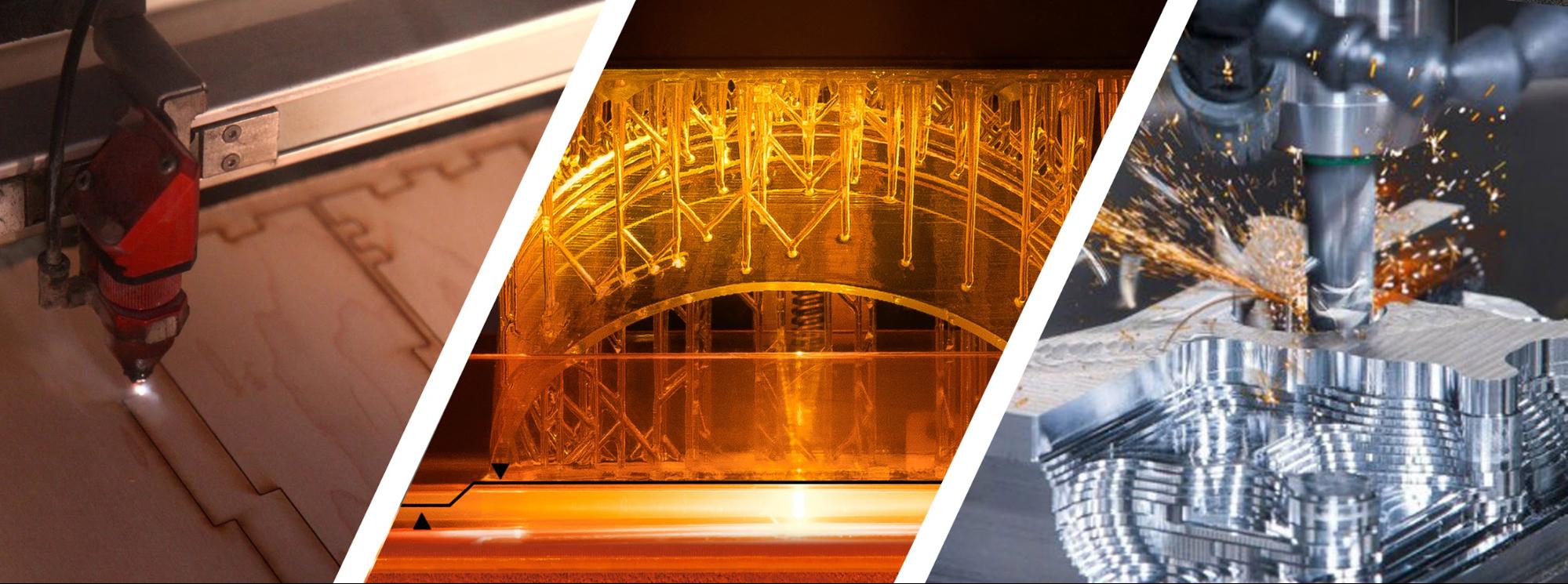
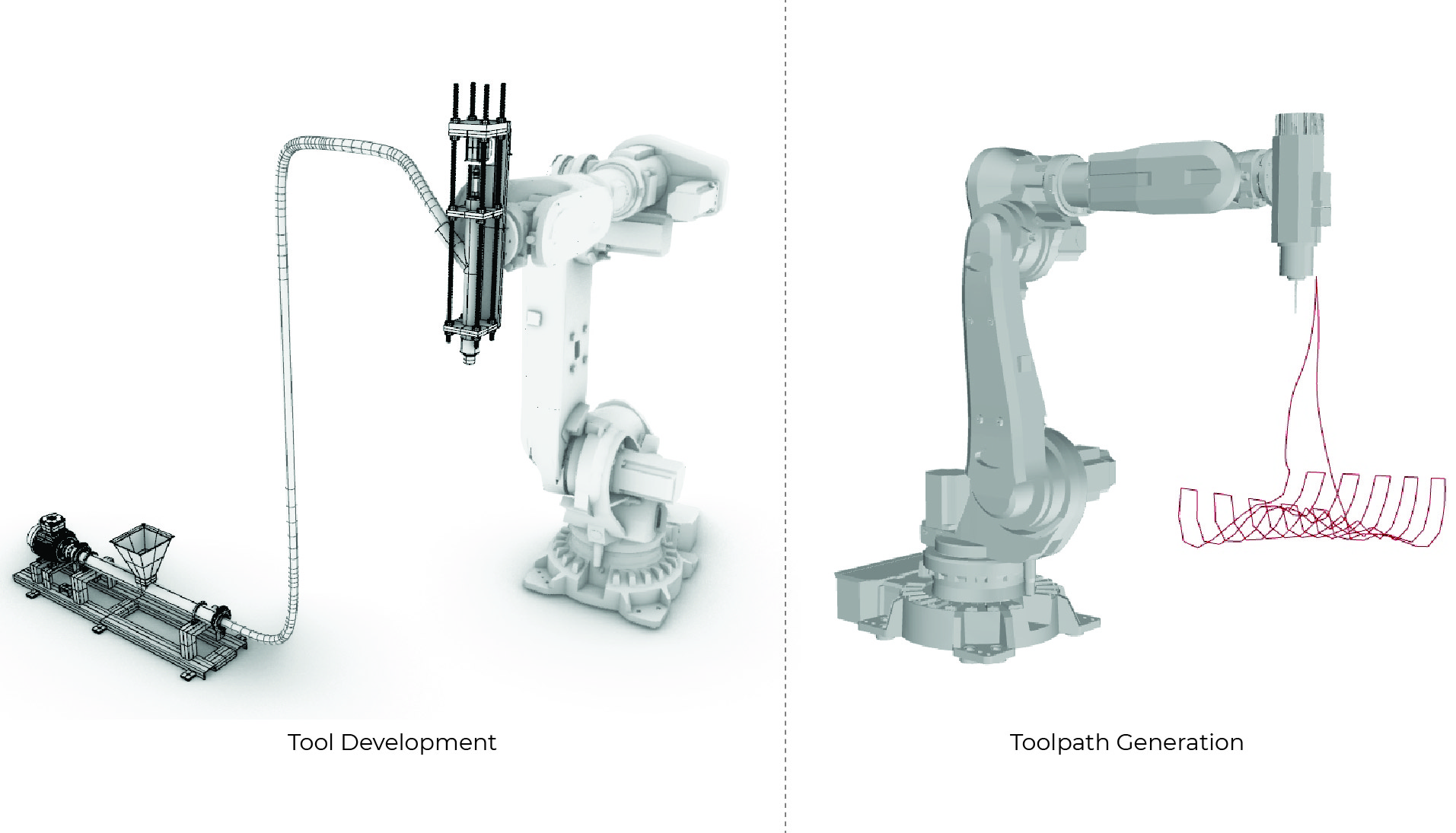